Bagnall Bricks
It seems that as well as building much of Wakefield, much of what it was built from was made locally, in two (or more) brickworks. Mount Clay Brick Works and Wind Hill Brick Works.
These aerial photos from 1932 show Eastmoor and the dark chimneys of the two brickworks.
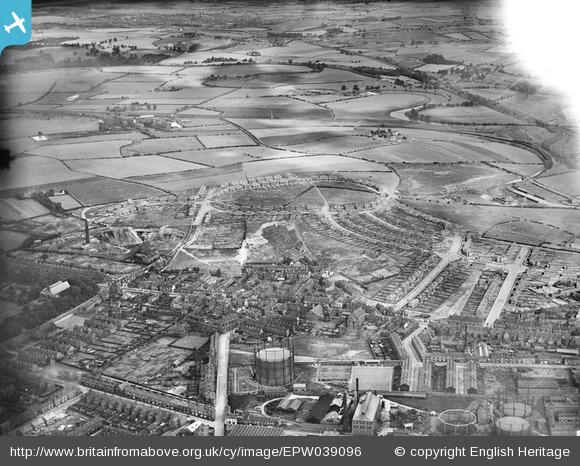
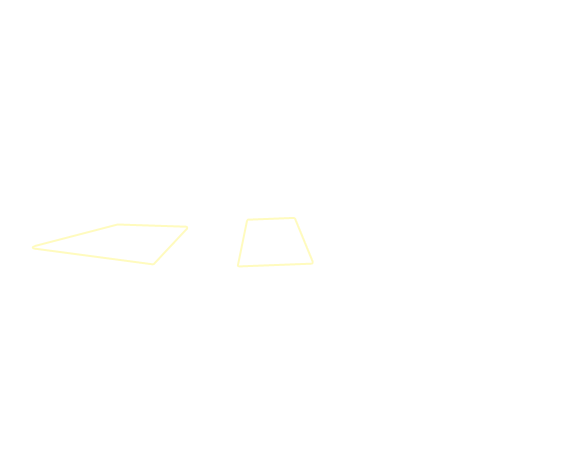
In this picture, it's hard to see the chimney of the Mount Clay Brick Works, but it is quite evident in the next two photographs.
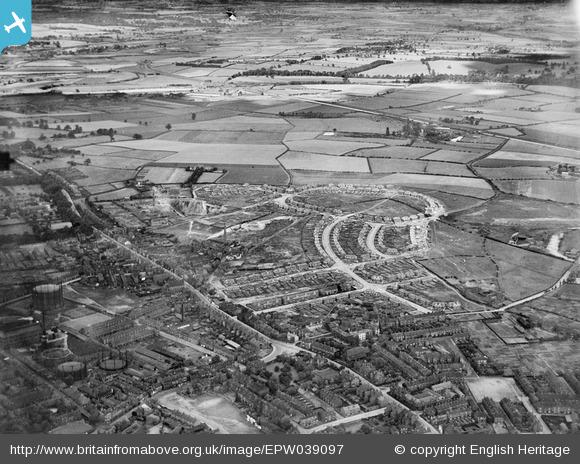
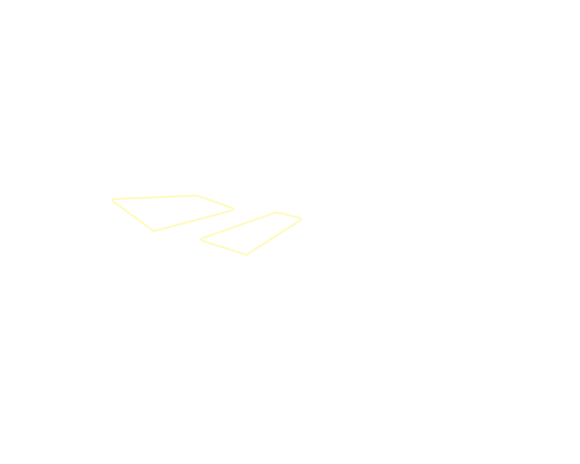
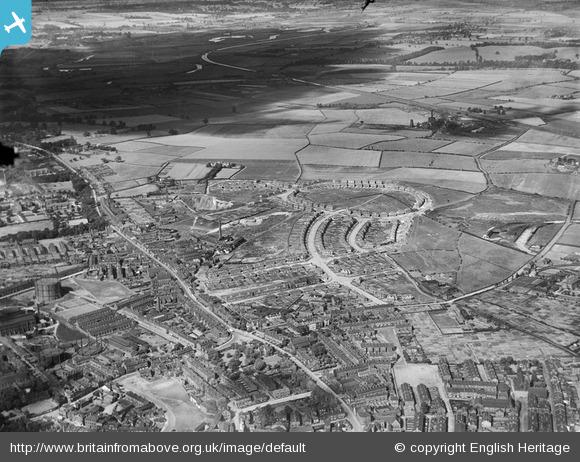
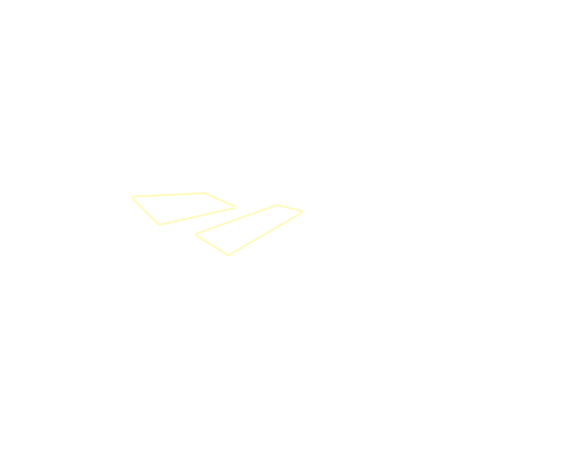
Mount Clay Brick Works
Map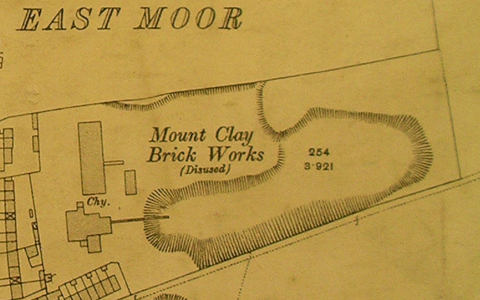
Mount Clay Brick Works, not far from much of the history of the Wakefield Bagnalls, shows like a scar on the landscape on old, Ordnance survey maps (See The Time Machine), and it seems it may at one time have been a brick factory run by the Bagnalls of Wakefield. Now, you would not guess it had ever existed as you look across the playing field which now occupies the space that the factory once did.
On the 7th April 1860 Messrs J and W G Kershaw brickmakers went bankrupt and their site and equipment was being sold by private contract at Greenhill road Eastmoor Wakefield, the purchaser was Mr Dunn Wakefield Councilor the name became The Mount Clay Brick Works, and he intended to update machinery and improve production due to the rise in building, The Mount Clay Brick Works - the above works for some time in the possession of our respected fellow citizen Mr Councilor Dunne, has through his enterprise and management, attained an importance among our local concerns which fully entitles them to special notice. At the best a brickyard is not a very attractive place to visit, but still it has its claims as an inspection of the above works will most convincingly prove. Here as in the case of other and even less presentable industrial undertakings, the advantages which ample capital and improved machinery and skill secure to the manufacturer are fully set forth. As our readers are aware the works are approached by Greenhill, a thouroughfare that of late years has been greatly improved. Entering the yard and taking in its area, and the works under it which include about four acres one is first struck by the entire absence of the usual features of a brick field. There are no moulds of clay in process of mixing and working by mud splattered labourers, no rows of low open walls of the fresh made product, straw thatched and constructed in lines the distance, between which are maintained with a mathmatical correctness. We observed no clay dashed manipulator at a trough up to his elbows in slush, kneading stuff with which the exactitude that long practice confers he just takes sufficient of to fill the mould. No attendant boy with deft like aptitude and clock like regularity slips the same from beneath the moulders hand, as the last time he passes it over the now formal brick. Non of these familiar objects meet the eye, instead we hear the busy clank of an engine, we see a machine with two ponderous cylinders revolving on a table crushing debris of some kind. Advancing up the yard still further we come upon an engine house, a group of kilns in process of erection, and the eye following the line of a narrow tramway lights upon the encarpment of a hill about 400 yards off, from whence sandstone and brine are being picked. So at last we have undisputed evidence of the locale, still the aspect is novel for a brickyard. Watching the labourers at the hill, we find they are busy filling small trucks which by their own momenta, not only carrying their proper load along the tramway incline, but also that of the attendant boy to whom not withstanding the constant indulgence, the ride seems exceedingly agreeable. The truck stops at the foot of another steep incline within a few yards of the machine house. Upon this incline a tramway runs which conveys the landed truck in to the shed, and here its contents are emptied into a large perforated iron pan, in which two cylinders of a ton each revolve and reduce the stone and brine to a state of powder. In this state the material is conveyed by a wooden trough to a system of tin elevators, these in turn deliver it to a machine by which, kneaded and moulded, the raw stuff that a few minutes ago we saw trucked along the tramway from the hillside is turned out a perfect brick, of the latest patent pattern. No greater contrast could be furnished to the old hand system of brick making, than the one here we descibe nor could any process of manufacture more strikingly illustrate how the application of machinery, while lessening manual labour and relieving it of the element of hardship, it but too often bears, makes both reforms conductive to increased production. There is a good impression, not unwarranted that home made have an advantage, over machine made articles, this is not so however in the case of bricks. The three objects to be attained in their manufacture, are ( a ) a reduction of the material to the fluest possible condition, ( b ) a thorough mixture and amalgamation of its constituents, and ( c ) the most powerful compression so that the brick while being moulded, is made as close as possible. It requires no argument to show, that not one of these processes could be carried out so effectively by hand as by machine. The pressure by the latter, equals some and it is only necessary to watch, Mr Dunns cylinders in order to be made equainted, with the marvellous degree of pulverisation to which the coursest debris may be reduced. Examining the bricks, in the large drying shed we find great quantities of them to be of various shapes, and of ornamental patterns, this speaks for an improvement in our domestic architecture. We have in the dutch an example of how brick can be utilised, in the way of aiding and working out architecture effects, and it is gratifying to find we are profiting by it. The superior material used by Mr Dunn, enables him to do full justice to this class of manufacture, and we have no doubt that under his skilful and enterprising management, it will arrive at still greater perfection. The machine which is the feature of the yard, is one of Craven,s patent - the very first our well known local firm turned out. It represents, the most improved brick making machine yet manufactured, and can produce thirteen or fourteen a minute, or in round numbers about 900 per hour. There are three kilns at work, capable of burning 30000 bricks each. The output of the yard has been for some times about 40000 to 50000 per week, the extensive contracts held by Mr Dunn, and the present satisfactory stir in the building trade, rendering this rate of production necessary. We understand that the spirited proprietor of the Mount Clay Brick Works contemplates still full improvements in his yard and developments in his business. We have only to add he has our best and most hearty wishes has he will of the most of those who know him, that the success he so fully deserves may crown his well directed efforts. Wakefield Free Press Saturday May 18th 1876.
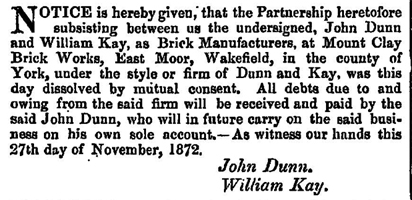
This notice from the London Gazette on 3rd December, 1872, mentions the passing of the brickworks from a partnership between William Kay and John Dunn into single ownership by John Dunn.
1909, 28th July Yorkshire Evening Post
WANTED, PIANO SCREEN, also a REPRESS: must be in good condition.-Bagnall Bros., Mount Clay Brickworks, Wakefield.
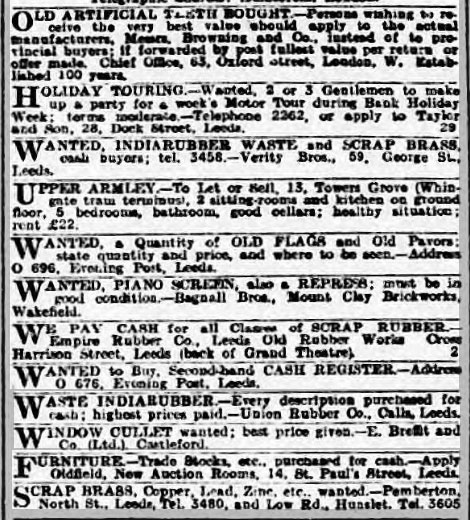
1909, 4th October Yorkshire Evening Post
To LET, HAULAGE of ONE MILLION BRICKS by traction or motor.-Apply Bagnall Bros., Mount Clay Brick Works, Wakefield.
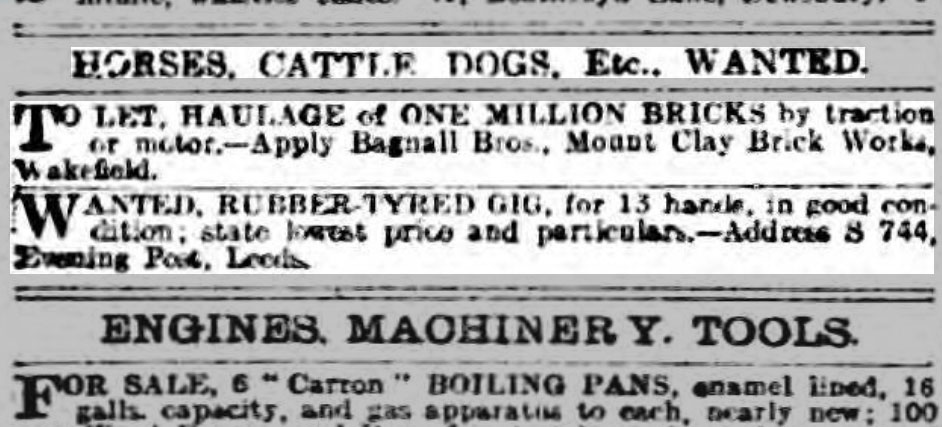
1910 William & George Dissolve Bagnall Bros.
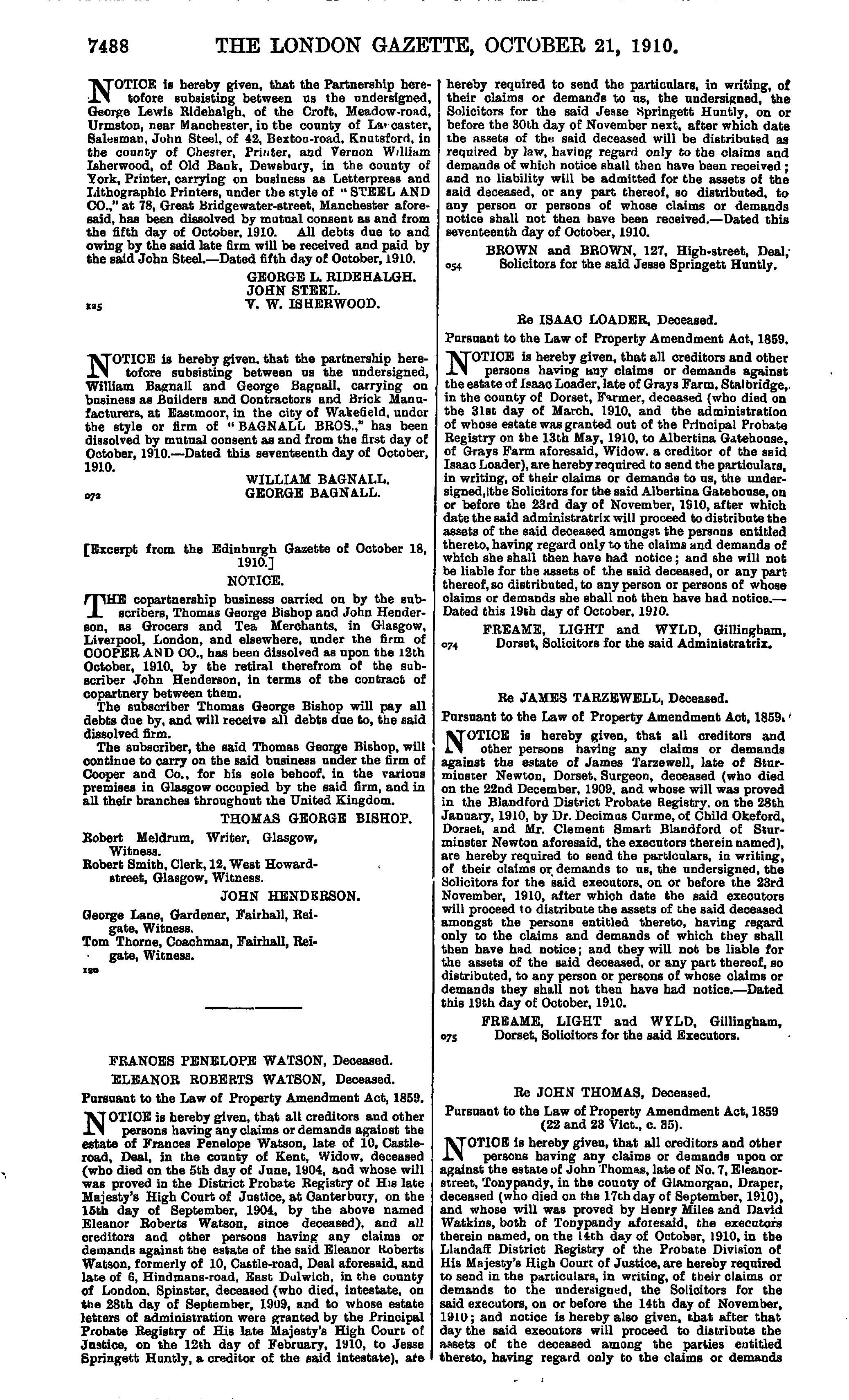
It seems that from this notice in the London Gazette, from October 1910, on 17th October, George and William Bagnall dissolved the firm "BAGNALL BROS."
This advertisement in the Yorkshire Evening Post on 21st August 1912 implies that the running, possibly the ownership of the brickworks was in the Bagnall family. Perhaps George teamed up with Harry?
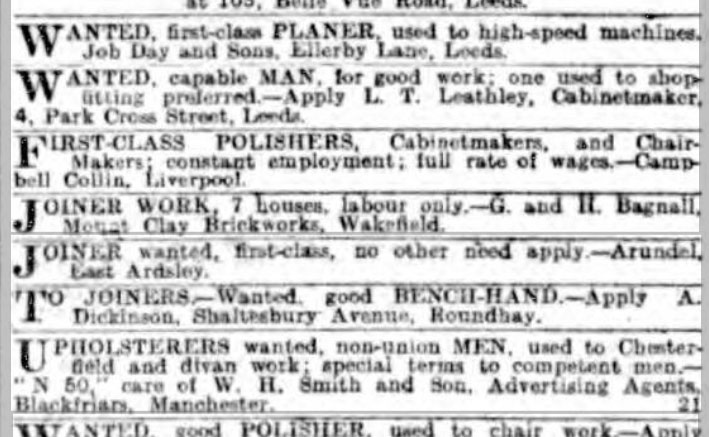
JOINER WORK, 7 houses, labour only, -G. and H. Bagnall, Mount Clay Brickworks, Wakefield.
It would be my assumption that this was George and Harry Bagnall.
This advert in the Official Wakefield Handbook, 1927, was brought to my attention by Dave Russ on the Wakefield Historical History Site (WHAS) a rich seam of historical information for the area. Thanks Dave.
Perhaps the Bagnall brick (Pictured at top) was made there, or at the brickworks in Accrington as related to me by - Margaret Johnson and - Michael Webster .
... they are Accrington brick. Grandpa did have a brick factory there and Granny had to run it for him in the 1st World War. He left her to do everything plus five children, two of which died. After the war I think he sold the brick factory so they would not have been his that he used on our house. Mother loved the red but I don't much like it, too shiny red!
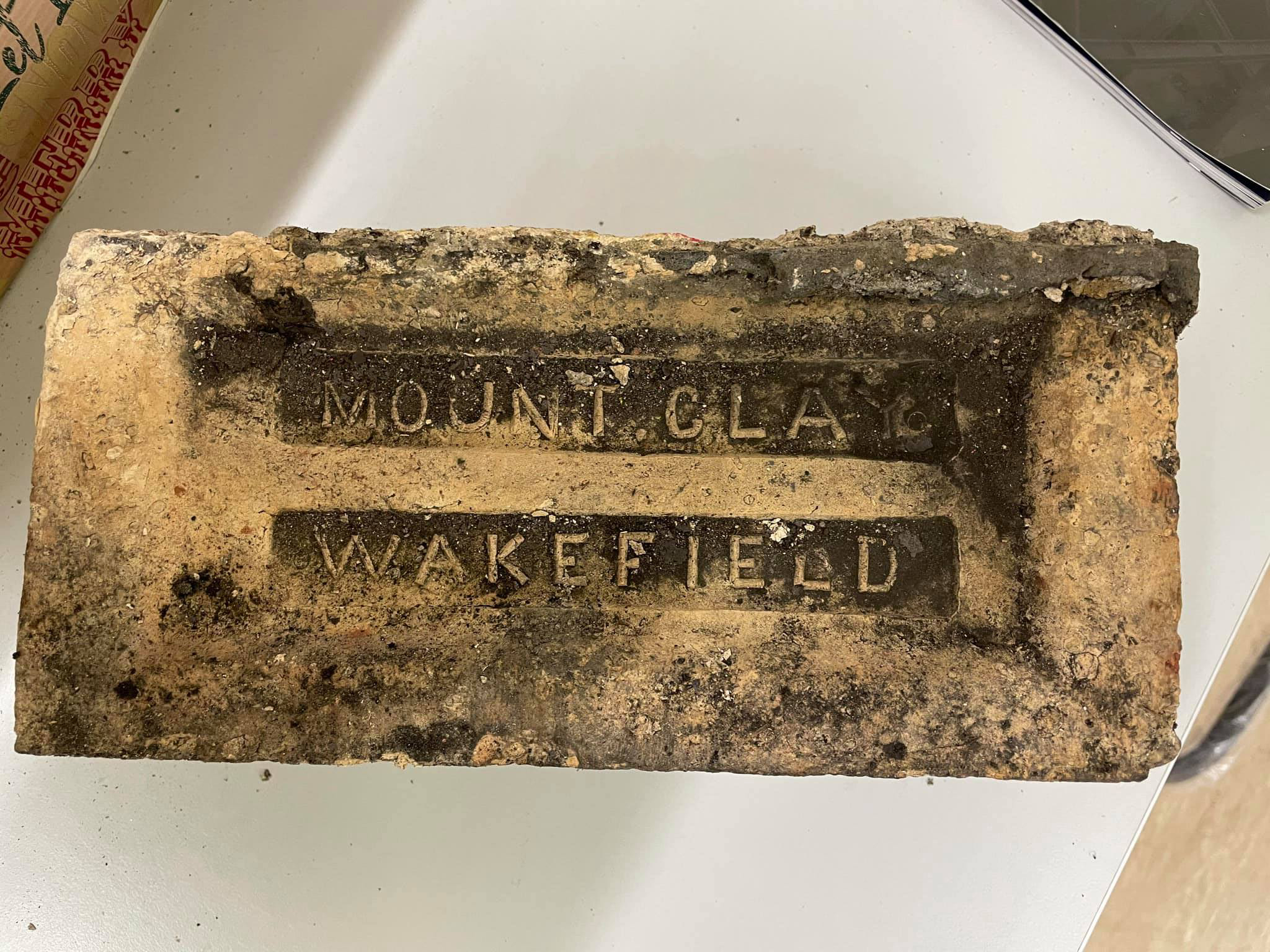
This brick, brought to my attention by Jonathan Webster, was certainly made there! Thanks Jonathan.
A Mount Clay brick also features on the Old Bricks - history at your feet website.
Wind Hill Brick Works
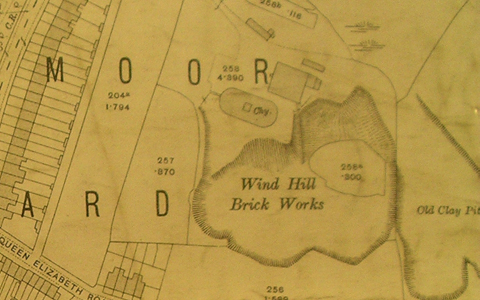
There is also nothing much left of the Wind Hill Brick Works except for an open playing field and several surrounding streets with names such as Wind Hill View and Wind Hill Close. - Michael Webster 's recollection below connects the Bagnalls with Wind Hill Brick Works.
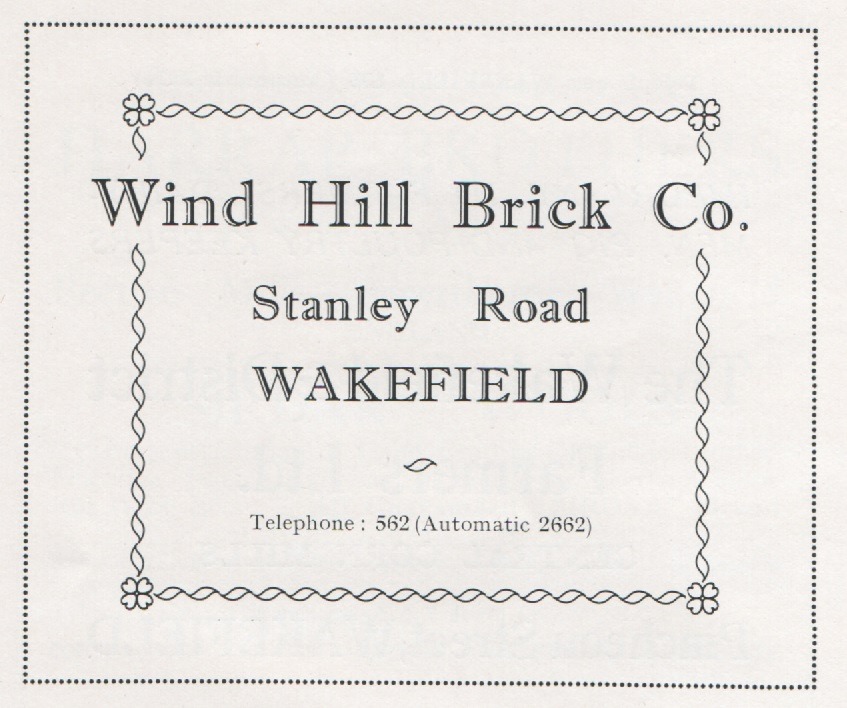
A couple of Wind Hill bricks feature on the Old Bricks - history at your feet website.
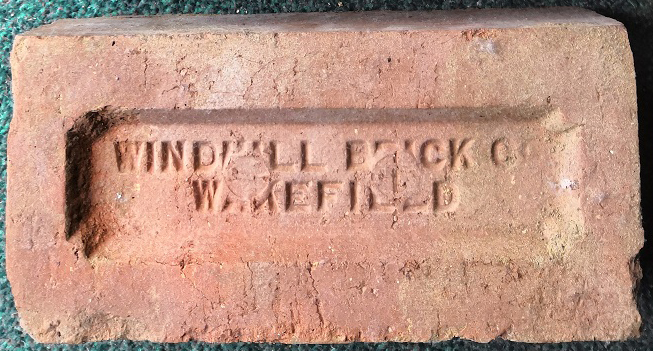
Grandpa made at least 2 sorts of bricks, both I think were made to the Accrington formula, the orange ones and the blue ones. If you tried to drill through the blue ones the end of your drill bit usually dropped off before you got the hole drilled. These were engineering bricks which when I lived at 401 Aberford Road consisted of all the internal walls and the inside skin of the external walls. His brickworks, as far as I remember was on Ivy Lane opposite the entrance to Stanley Royd hospital.
If he was building a large site, he made a brickworks on site, otherwise he had 70 pairs of horses and transported them to Kirkgate station, he eventually sold out to his friend Armitage Brickworks.
The Normanton brickworks have a vast collection of bricks, that's if they're still in business.
Grandpa's bricks are still evident after aprox 100 years and are all over Stanley and a lot of the schools he built are still going strong.
He built most of Beeston area of Leeds which have been converted from back to back terrace houses to through terraces with Marble looking fireplaces and the ones that I have been in are in excellent condition.
Bagnall Brothers was Uncles Jeffrey & Roland, Grandpa was Geo Bagnall, possibly & son.
There is also a sample Bagnall Brick on the Old Bricks - history at your feet website.